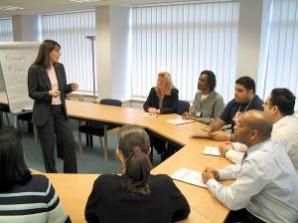
If you've been having trouble sleeping, the perfect solution might be a 101-page OSHA training requirement manual. For the rest of you, here are some OSHA requirements from their Standards and Training Manual broken down into digestible chunks.
Easily digestible chucks aren't totally inclusive. Specific OSHA training requirements and standards apply to your unique industry. Always check with OSHA for the latest news on training requirements for your particular business.
OSHA Background
The Occupational Safety and Health Administration (OSHA), sets many standards for employers and workplaces. They do this for the welfare and safety of employees but it can seem overwhelming if you're an employer.
OSHA's standards reflect their belief that training is essential for employee safety and health in the workplace. Studies back OSHA up. Research reports that new workers (with less training) have more accidents and injuries on the job than do seasoned employees.
Keep in mind that training your employees will not only keep you and everyone else safe, but you're also protecting the welfare of employee families and saving your business money. A safe workplace is a less expensive workplace in terms of insurance, workers comp, and re-hiring expenses.
Some general standards that OSHA sets for employers include:
- It's the employer's responsibility to fit proper employees to proper jobs.
- This can be based on employee experience, training to date, certification, or be based on physical limitations. Such as don't hire someone with a bad back or fear of heights to climb ladders frequently - that would be a poor hiring decision.
- Current employee safety and health trainings and evaluations of these training must be up-to-date.
On a side, but important note, it's wise to keep records of employee trainings. Certain trainings such as CPR or blood borne pathogen safety are federally required so records are always kept. But what if your employee gets cut on a band saw? An accident investigator will ask, "Was this employee trained on band saw use and can you prove it?" Cover your back and keep good records.
Use the OSHA Training Requirement Model to Develop a Plan
OSHA training guidelines follow a model designed to be easy for both big companies and small business to follow without hiring a safety expert or buying expensive training materials. This model is completely adaptable to an employer's specific business.
According to OSHA this model includes the following steps:
Step One: Determining if Training is Needed
First, determine if training can even solve a workplace issue. It often can but not always. For instance, if toxic fumes are harming employees, no amount of training will stop the fumes -- in this case proper safety protective gear or removing the fumes are the only safe steps to take.
Step Two: Identifying Training Needs
Job Safety Analysis (JSA) forms are very useful in determining where training is needed. If you haven't worked with JSA forms yet check out this University Job Safety Analysis Manual article which will explain in detail how to do so. You can also determine where training is needed by:
- Trainings must combine established goals and objectives.
- Trainings should be evaluated for positive outcomes. If positive outcomes are not met, trainings need to be revised and employee must be re-trained. Another option is to conduct frequent trainings on the same topics.
- Looking at past accident reports
- Having employees tell you where they think training is necessary
- Checking out businesses that are similar to yours and asking about their training procedures
Step Three: Identifying Goals and Objectives
Trainings should focus on areas where improvement is actually necessary. If all your employees have good hygiene skills, why waste time re-training hand-washing. Focus goals and objectives on issues that will improve the workplace.
- Write out a list of goals and objectives.
- If you're training on a process (like band saw use) write out all steps in order so you don't miss important details that should be included.
Step Four: Developing Learning Activities
This step includes planning the perfect employee training.
- Choosing methods and materials for training is the fun part. You can pick materials like books, PowerPoint presentations, quizzes, and free workplace safety videos.
- Figure out if outside help is needed and if you can afford it. Something like driving safety at work you can likely handle yourself. But do you have the expertise to conduct CPR or teach employees how to deal with electrical currents? Hire outside safety experts when necessary.
Step Five: Conducting the Training
This step is often daunting if you've never taught trainings before. Here's how to break it down and make it easier:
- Provide overviews of all materials at the start of training.
- Make sure you relate the skills or information you're teaching to your employees working goals and experiences.
- At the end of the training reinforce the training by going back over key objectives and safety tips.
- Be sure to include hands on experience. If you're training on that band saw - take everyone out to the workshop. If you need employees to know how to properly wear medical protective clothing get that clothing out.
Step Six: Evaluating Training Effectiveness
Three simple things will tell you if training works.
- Employee questionnaires
- Supervisory reports on employee knowledge
- Workplace improvement
- This means that there should be evidence of fewer accidents or injuries overall.
Step Seven: Improving the Program
If an evaluation shows little to no workplace safety improvements ask:
- Were training materials confusing?
- Was something missing?
- What did employees learn vs. what they didn't - where were the difference in technique between the two.
Whew, You Made It! But...
There's always a chance you'll need to revise and re-train. Follow the same OSHA training requirement model steps but try to be more complete in the planning stages. If necessary call OSHA representatives in your state to get expert help. Learn more about state requirements and find resources at OSHA's site.